
TRACE 3D: Electromechanical 3D Printing
Mechanical Engineering Senior Design
Project Timeline: September 2020 - April 2021 (7 months)
Team Role: Design Lead
Awards: Jerome Fisher Management & Technology Program Integration Lab Award
Project Objectives & Results
Hobbyists and professional makers desire complete design and creative freedom while prototyping. Most of their projects involve both mechanical and electrical components, especially highly functional electronics such as printed circuit boards (PCBs). Integrating conventional mechanical systems with PCBs often leads to prototypes that are built suboptimally, are time-intensive to assemble, and are expensive.
Trace3D was the product of a yearlong senior design course. Together with four other Penn students, I designed a proof-of-concept electromechanical 3D printer that uses off-the-shelf materials to create physical prototypes that integrate insulative structural components and conductive pathways in three dimensions. Essentially, Trace3D is a 3D printer for circuit boards. Beyond flat circuit boards, circuit boards in any shape imaginable, with electronic elements embedded into the structure, can be created. Designers are free from the constraints of traditional flat PCBs, leading to increased design freedom and simplified development cycles.
A one-dimensional test gantry, seen below, was used to experimentally determine values for the essential properties of feed rate, build speed, extrusion temperature, channel radius, nozzle to build plate height, nozzle aperture, and trace resistance. Once materials and alloys of interest were selected, an iterative testing procedure was accomplished by using test wafers and systematically varying these parameters.
Once findings from the one-dimensional tests were synthesized and solder deposition was fully characterized, we moved on to testing using a 3D implementation gantry. This testing and associated custom software and G-Code development culminated in the production of a “drone totem”; a representative first print.
The first picture is a representation of a possible final system form of this printer. Unfortunately due to the COVID-19 pandemic, this entire project was undertaken remotely, without access to engineering facilities. As such, the project was scoped to only a basic prototype for the system. This prototype is the second picture in this section, which includes an Ender 3 Pro with a custom extruder stack-up for the conductive material (solder) and a second extruder addition powered by the Ender IDEX system for the insulative material (PLA).

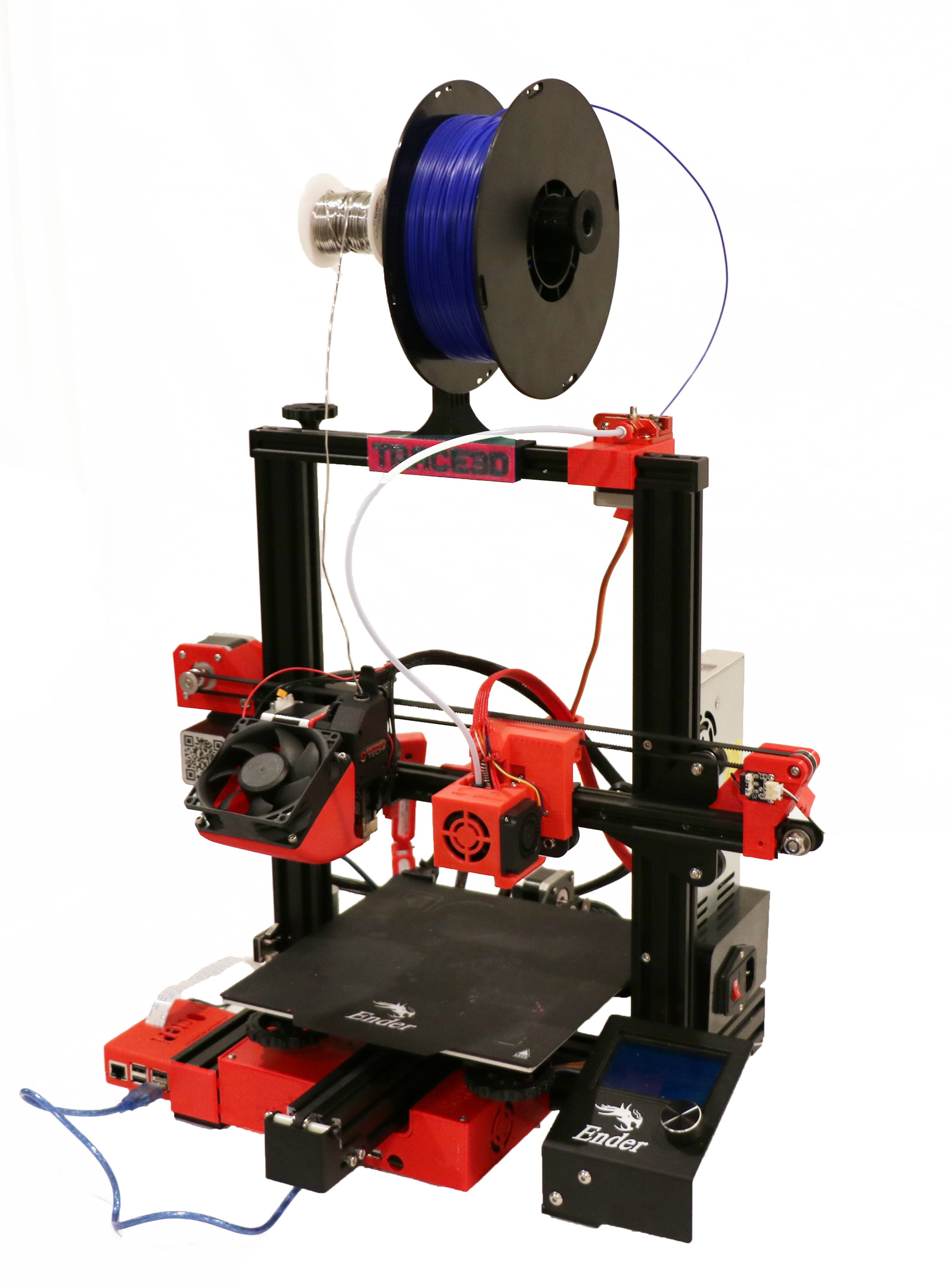
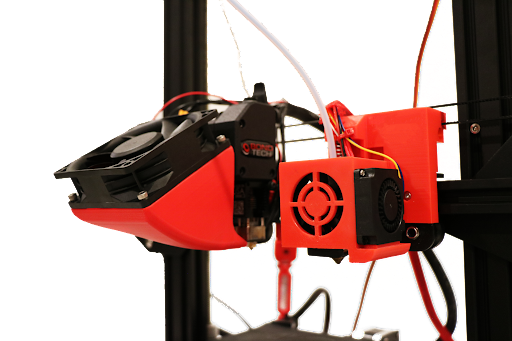
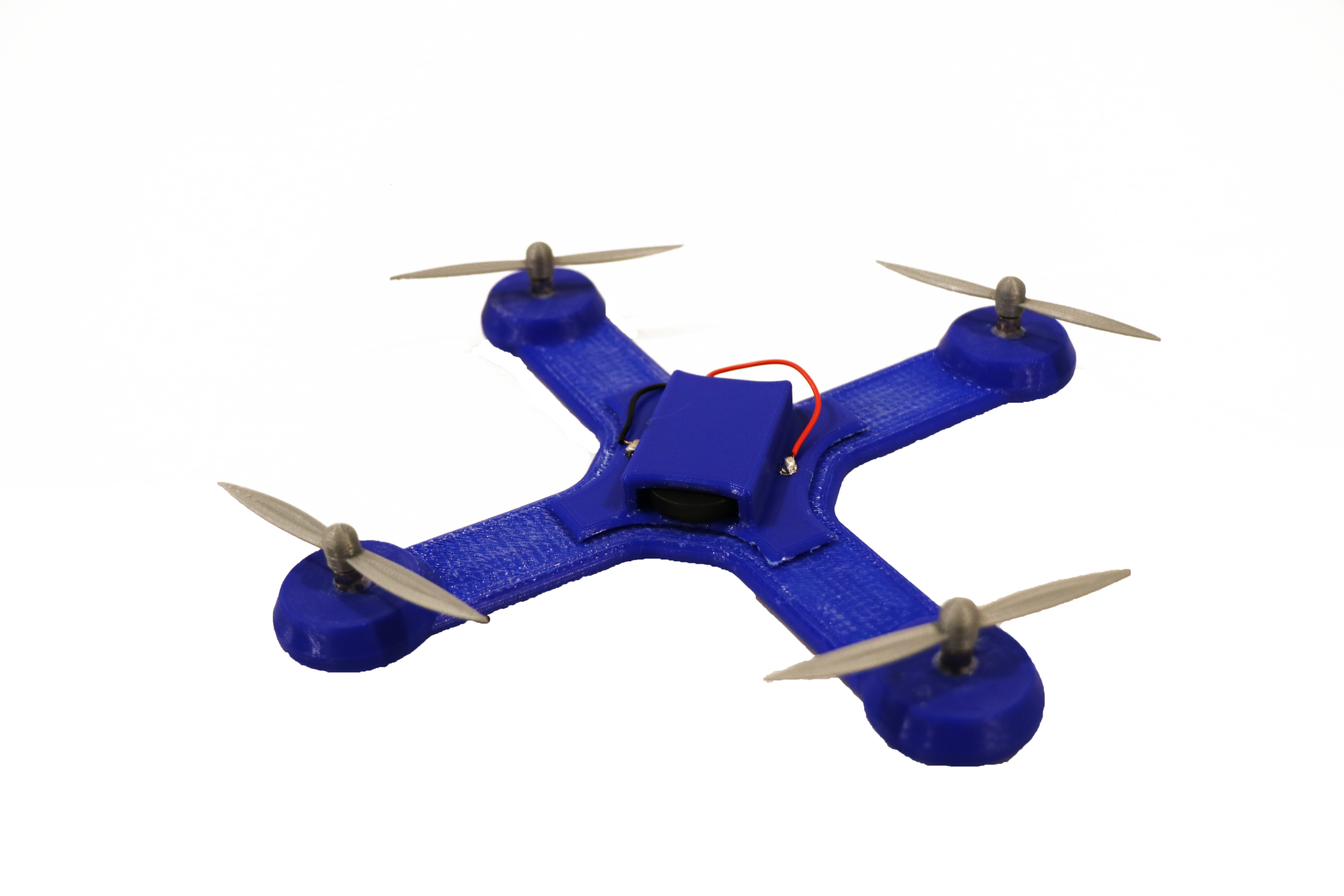

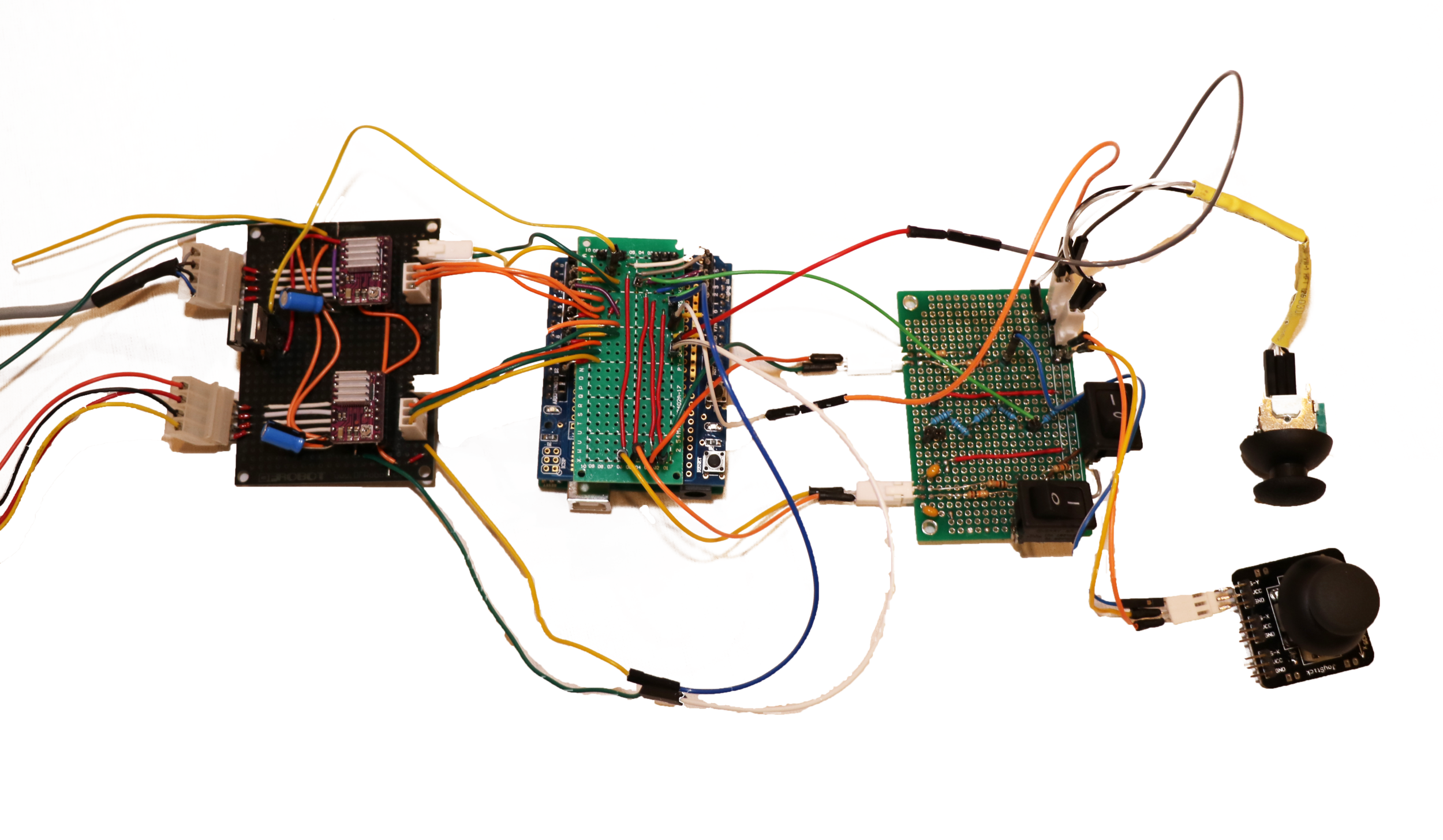

TRACE 3D In Action
The video on the left shows the complete development process of our drone totem.